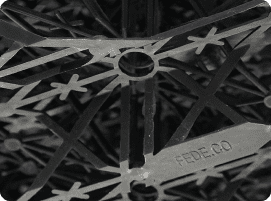
Plastic injection moulding is a cornerstone in modern manufacturing, enabling the mass production of high-quality plastic components across various industries. From automotive parts to consumer electronics, this versatile process delivers precision and efficiency. But what exactly is plastic injection moulding, and how can it benefit your business? In this guide, we’ll break down the process, explore the materials used, and highlight its numerous applications.
What is Plastic Injection Moulding?
Plastic injection moulding is a manufacturing process where melted plastic is injected into a mould to form a specific shape. This process is ideal for producing large quantities of identical parts with high precision. Below, we explore the key stages involved in the process:
• Clamping: The mould halves are securely closed and held together by a clamping unit.
• Injection: Molten plastic is injected into the mould cavity under high pressure.
• Cooling: The plastic cools and solidifies, taking the shape of the mould.
• Ejection: The mould opens, and the finished part is ejected.
Materials Used in Plastic Injection Moulding
The choice of material in injection moulding depends on the product’s intended use. Common materials include:
• ABS (Acrylonitrile Butadiene Styrene): Renowned for its toughness and impact resistance, making it ideal for automotive and electronic components.
• Polypropylene (PP): Known for its chemical resistance and flexibility, often used in packaging and medical devices.
• Polyethylene (PE): Valued for its durability and cost-effectiveness, used in everything from bottles to piping.
Applications of Plastic Injection Moulding
This process is highly versatile, making it suitable for a wide range of industries:
• Automotive: Dashboards, bumpers, and interior components benefit from the strength and precision of injection moulding.
• Medical Devices: The ability to produce high-precision parts makes it ideal for creating syringes, surgical instruments, and diagnostic equipment.
• Consumer Goods: From plastic containers to electronic housings, injection moulding is essential for producing consistent, high-quality consumer products.
Advantages & Disadvantages of Plastic Injection Moulding
Advantages:
• High Production Efficiency: Capable of producing large quantities quickly.
• Consistency: Delivers precise, repeatable parts with minimal variance.
• Versatility: Supports the use of multiple materials in a single process, such as overmoulding.
Disadvantages:
• High Initial Costs: The upfront investment for mould creation can be significant.
• Potential for Defects: Issues like warping or short shots can occur if the process isn’t meticulously controlled.
Expert Tips for Optimising Plastic Injection Moulding
• Material Selection: Always choose materials that match the intended use of the product.
• Process Control: Monitor the temperature, pressure, and cooling times closely to avoid defects.
• Design for Manufacturability: Ensure your product design is optimised for injection moulding to reduce production costs and improve efficiency.
Conclusion
Plastic injection moulding is a powerful tool for any industry requiring the mass production of high-quality plastic parts. By understanding the process, materials, and applications, you can make informed decisions that enhance your manufacturing capabilities. Ready to take your production to the next level? Contact us today to discover how our plastic injection moulding services can meet your needs.
Have specific questions or a project in mind? Reach out to our team for a consultation and let us help you bring your ideas to life!